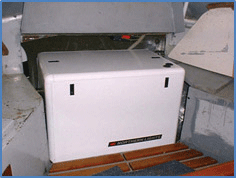
When I set out to write this blog piece I thought it would be a simple matter of writing about sound enclosures, construction materials and noise reduction. However, when I started researching these areas I quickly realized there is too much material for a single blog to be meaningful. This is therefore the first in a series of blogs on the topic of noise reduction for generators.
Part 1 – Noise
With the continued and expanding use of diesel generator sets there has come an increased focus on controlling the noise these generators create. Whether generator sets are located in enclosures outside a facility or home, inside, on the roof or even on a yacht, designers are making more efforts to control generator set noise and vibration in order to reduce the effects on neighbours and building occupants alike. Whether generator sets run continuously in prime-power applications, intermittently in demand response applications, or occasionally in emergency standby situations or testing, their operating sound levels nearly always require remediation due to market requirements.
In order to understand the solutions to reducing noise from generators, it is first necessary to understand noise. Therefore this blog provides a simple summary of noise and its characteristics, and the sources of noise created by generators.
What is Noise?
Vibrating objects induce pressure waves that travel through the air, reaching our ears as sound. Noise, by definition, is simply undesirable sound. When the amplitude of the pressure waves becomes too high, the amount of sound becomes uncomfortable. In addition to being annoying, excessive sound can cause permanent hearing damage. The following diagram explains the physiology of what happens when sound reaches the human ear.
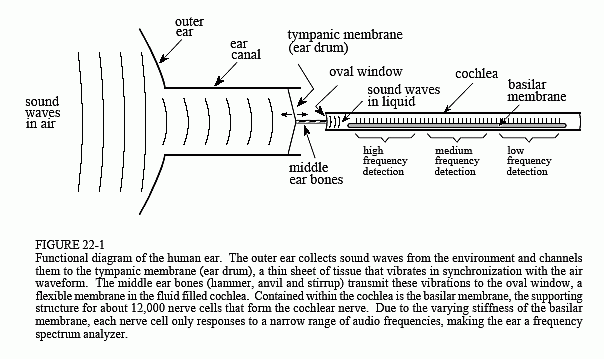
The human ear has such a wide dynamic range that the logarithmic decibel scale (dB) was devised to express sound levels in a convenient way. The ratio between the softest sound the ear can hear and the loudest sound it can experience without damage is approximately a million to one. By using a base-10 logarithmic scale, the whole range of human hearing can be described by a more convenient number that ranges from 0 dB (threshold of normal hearing) to 140 dB (the threshold of pain).
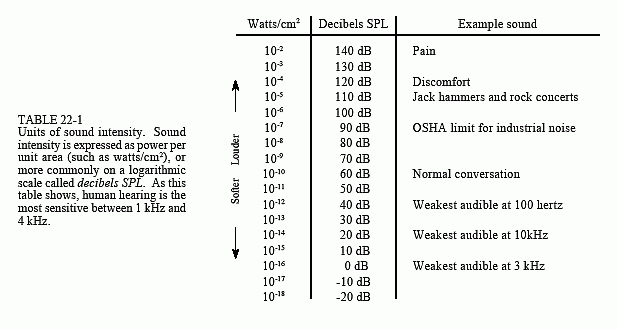
There are two dB scales used to describe sound: A and L.
- The dB(L) scale is linear and treats all audible frequencies as having equal value. However, the human ear does not experience all frequencies the same way. Our ears are particularly sensitive to frequencies in the range of 1,000 to 4,000 Hz, and they are less sensitive to sounds in lower or higher frequencies. (This is why dogs often start barking for reasons humans don’t understand – dogs have the ability to hear sounds of a much higher frequency than humans)
- To adjust the sound pressure levels to more accurately reflect what the human ear perceives, the frequency-weighted dB(A) scale has been adopted as the official regulated sound level unit.
It is also worth noting that the db(A) scale represents an “absolute” value. For example, stating that a generator produces 98 db(A) of noise isn’t particularly meaningful – remember by definition it can only be noise if it is undesirable to the recipient. Standing alongside a generator generating 98 db(A) of noise is completely different to standing 500 meters away (where it probably couldn’t be heard).
More useful therefore is to state at what distance from the generator the noise level is experienced. As a result most generator manufacturers state sound levels in terms of db(A) @ x meters, for example 85 db(A) at 1 meter. This in turn presents challenges in terms of measurement, but that is a topic for a later blog.
Sound produced by generator sets
The principal sources of noise from generators are described below.
1 Engine mechanical noise
With the advent of high-pressure common rail fuel injection, advanced turbocharging and better combustion control, manufacturers have significantly reduced overall mechanical noise from diesel engines. The amount of sound varies with the size of the engine and its load, and can be as high as 110 dB(A) measured at one meter. Engines with more cylinders have more power strokes per revolution and therefore deliver a smoother flow of power with less vibration. Smaller engines tend to be harsher in operation and produce more noise and vibration for their size.
2 Exhaust noise
Engine exhaust is a major contributor to overall sound levels. When measured without an exhaust silencer noise can be 120 dB(A) or more depending on the size of the engine. The sound level can be reduced by up to 40 dB(A) depending on the silencer employed.
3 Cooling fan noise
Sound emanates from turbulent air as the cooling fan moves air across the engine and through the radiator. The amount of sound varies with the speed and volume of air being moved as well as with the design and distortion of the fan blades. The amount of sound can be as high as 95 dB(A) at one meter.
4 Alternator noise
The alternator has an internal cooling fan, and the combination of cooling air movement and brush friction produces noise. However, the sound level is always small compared to the driving engine.
5 Induction noise
Current fluctuations in the alternator windings create mechanical noises that add to total noise when load demand changes.
6 Structural/mechanical noise
This is caused by mechanical vibration of various structural parts and components that is radiated as sound. Isolators between the engine, alternator, controls and other components help to reduce the amount of vibration that gets converted to noise. Anti-vibration mounts can also be employed to reduce noise propagation through the ground or hull where the generator is located.
Summary
In this first blog we have introduced the definition of noise, described its impact on human beings and highlighted the sources of noise from generators. In the next blog we will discuss methods for attenuating these noise levels.
Images courtesy of http://conocimientosamplifiersfr.blogspot.com.